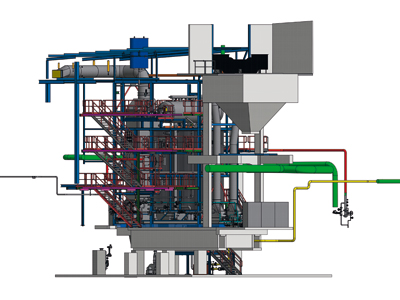
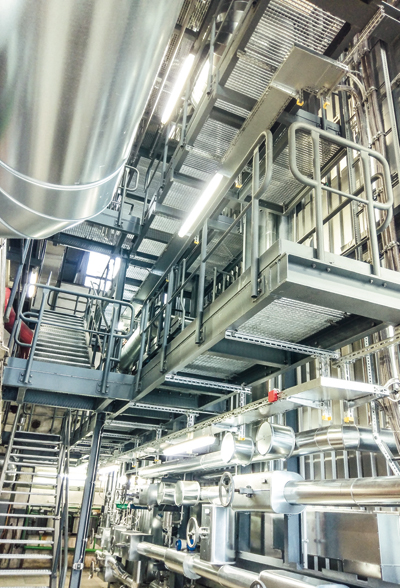
Ein neuer Wasserrohrkessel für WMF
Am Hauptsitz Geislingen an der Steige betreibt die WMF Group in Eigenregie ein zentrales Kraftwerk, das Elektrizität und Dampf erzeugt. Die produzierten Energiemengen sichern am Campus die Versorgung der Produktion und Entwicklung, der Marketing-, Test- und Schulungsbereiche sowie der Verwaltungs- und Outlet-Flächen. Mit Hochdruck arbeitet M&P im Projektteam der WMF vor Ort an einem neuen Dampfkessel, der die Energieversorgung am Standort zukunftssicher machen soll.
1853 nimmt die Metallwarenfabrik „Straub & Schweizer“ im badenwürttembergischen Geislingen an der Steige ihren Betrieb auf. Und von Beginn an ist klar: Der Energiehunger der Produktion kann nicht allein mit der Versorgung aus öffentlichen Netzen gestillt werden. Seit über 160 Jahren erzeugt deshalb ein hauseigenes Kraftwerk neben Wärme (in Form von Dampf) auch Elektrizität. In der Gründungszeit erfolgt dies in einem Wasserdampf-Kreislauf (Dampf treibt Turbine zur Stromproduktion an und verrichtet dann im Werk seine Heizarbeit). Nach dem gleichen Grundprinzip stellen heute zwei zentrale Wasserrohrkessel lastabhängig Dampf bereit, der in einer von drei Dampfturbinen Elektrizität erzeugt und dann als Abdampf das Werk mit Prozess- und Raumwärme versorgt. Auch wenn das Verfahren gleich geblieben ist: Was als Kessel 1 mit Kohlefeuerung begann, hat sich über den Einsatz von Schweröl heute zu den Kesseln DK 8 und DK 9 mit einer kombinierten Feuerung aus Erdgas (Regelbrennstoff) und leichtem Heizöl (Besicherung/Notbetrieb) gewandelt.
Dampfkessel DK 10 – das Projekt
Dass nach mehr als 160 Jahren bisher lediglich der neunte Dampfkessel installiert ist, zeugt von einer gezielten Instandhaltung der Technik. Trotzdem ist der Kessel DK 8 nicht mehr zukunftsfähig: Errichtet als gemauerter Wasserrohrkessel mit einer Kohlerostfeuerung und umgebaut auf die aktuelle Gebläsefeuerung, entspricht der gealterte Kessel in Bezug auf Effizienz, Emissionen, Regelbarkeit und Lastverhalten nicht mehr den heutigen Anforderungen. Das Zählrad der Kesselnummern dreht sich einen Zacken weiter: Der Dampfkessel DK 8 mit seiner Leistung von 25 t/h wird durch einen neuen Wasserrohrkessel mit Membranwänden, emissionsarmer Zweistofffeuerung und gleicher Dampfleistung ersetzt. Und da die Nummerierung des Kessels feststeht, hat auch das Projekt gleich einen Namen: Dampfkessel DK 10.
Dieser wird mit einer vertikalen Brennkammer, stehenden Heizgaszügen und Zweibrennerbetrieb als Bodenfeuerung produktionsbegleitend errichtet und in Betrieb genommen. Mehr als zweieinhalb Jahre begleitet die M&P Gruppe das Projekt von der Spezifikation des Kessels über die fachtechnische Betreuung des Ausschreibungsverfahrens (Kesselhersteller als Technik-GU mit schlüsselfertiger Übergabe) bis hin zur Unterstützung im Genehmigungsprozess.
Mit Dampfkessel 10 in der Champions League
Obwohl der neue Wasserrohrkessel aus deutscher Fertigung (Firma Wulff & Umag aus Husum) und mit modernster Feuerungstechnik (Firma Walter Dreizler aus Spaichingen) Hochdruckdampf von 450 °C erzeugt, spielt er in Bezug auf die Effizienz in der Champions League und unterschreitet mit seinen Emissionen nach Vorgabe der WMF die gesetzlichen Rahmenbedingungen deutlich – jederzeit im alltäglichen Dauerbetrieb. Zusammen mit der geforderten Flexibilität zur Laständerung ist ein Kesselsystem entstanden, das dem Wandel der Energiemärkte heute und morgen in hohem Maße entsprechen kann. Mit seiner zukünftigen Aufgabe als Führungskessel stellt der DK 10 eine Energiemenge bereit, die der Versorgung von ca. 5.000 Haushalten mit Strom und Wärme gleichkommt.
Dabei herrscht im Inneren ein Druck, der einer stehenden Wassersäule von ca. 500 m entspricht – und dies bei materialfordernden Temperaturen von über 450 °C. Dass bei diesen Extremwerten auch noch die Umweltbelastung reduziert wird, komplettiert das Gesamtbild einer beispielhaften Anlage: Gegenüber dem zur Stilllegung anstehenden Kessel DK 8 werden die Schadgasfrachten um mehr als 20 % reduziert. Und der verminderte Ausstoß an schädlichem Kohlendioxid entspricht der Arbeit eines gewachsenen Laubwalds von mehr als 800 ha.