The scope of services of M&P
- Digital service provider management, commissioning, feedback and billing
- Establishment of paperless end-to-end business processes (paperless maintenance)
- Implementation of a future-proof technical SAP infrastructure for maintenance, purchasing, controlling and finance
- Set-up of an SAP service provider portal
DFS Deutsche Flugsicherung GmbH is responsible for air traffic control in Germany. Since 2014, M&P BEGIS GmbH has been driving the company’s digital transformation in the field of maintenance.
DFS Deutsche Flugsicherung GmbH is a company under private law that is 100% owned by the German federal government. On behalf of the federation, DFS carries out air traffic control tasks in accordance with the German Aviation Act (Section 27c, para. 2). DFS has controlled civil aviation and, in peacetime, military air traffic since 1993, though this does not apply to military airports. DFS is represented at a total of 15 international airports throughout Germany and at 9 regional airports through its subsidiary DFS Aviation Services GmbH. Air traffic control in the towers and control centres is part of its core business.
Transparency through digitisation
The Maintenance Solutions team, led by Simon Krienke, is, among other things, responsible for the digital transformation of maintenance at DFS in the Systems and Infrastructure Services division. As far back as 2014, the experts initiated the Paperless Maintenance project to digitise maintenance in technical building management (TBM). The goals were to digitise processes, increase data quality, gain data sovereignty, facilitate verification and increase transparency of the services from external providers. In addition, a consistent, paperless end-to-end business process was established.
The entire process of service provider management was to be made transparent so that the degree to which the service has been provided can be shown for each tender and the verification of the services provided can be carried out more effectively. The replacement of flat-rate remuneration for TBM services and the establishment of order-related billing per service provided were core aims of the project.
Technical SAP infrastructure from M&P BEGIS reaches new heights
Based on the existing SAP infrastructure with the modules Plant Maintenance (PM), Materials Management (MM), Controlling (CO) and Finance Accounting (FI), M&P BEGIS GmbH implemented management of external service providers for the TBM and automated the commissioning, verification and billing of orders as far as possible. In this context, a new technical location structure adapted to the requirements of DFS and corresponding to the regional structure of DFS technology was introduced, together with standardisation of the stock lists. Significant savings were achieved as a result – for example by switching from flat-rate remuneration in the area of maintenance and inspections for technical systems or from individual remuneration for the provision of maintenance and inspection services.
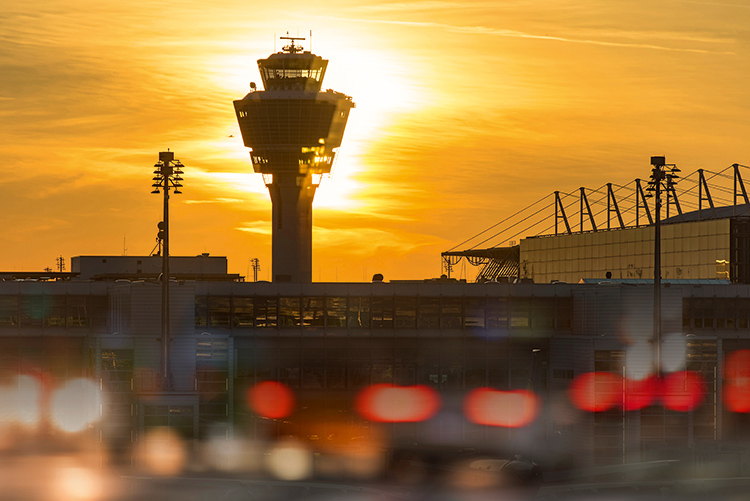
Trendsetting: the SAP service provider portal
The goals were achieved with the SAP service provider portal from M&P BEGIS GmbH, which makes orders for services created in SAP available online. The service provider can access, edit and confirm the orders and additional information there. In SAP, the confirmations are automatically assigned to the respective purchase order and the underlying task. Recorded documents such as maintenance and test logs are stored in SAP in such a way that they can be found via the corresponding facility.
The front-end component of the solution is based on the UI5 framework. The presentation layer makes it possible to edit SAP-based facilities through interaction elements. These elements are tasks, purchase orders, messages and documents that are required as part of the implemented assignment process. The user can confirm assignments by specifying a deadline and optionally enter a follow-up message for a technical facility. They also have the opportunity to view all documents stored that relate to a task and to file new documents as part of the commissioning process, e.g. test reports. In addition, they can obtain order documents and information on the technical systems, provided that they have been granted approval.
In addition to the delivery of the front-end component, the settings necessary for the functionality and customisation were implemented in the back end.
With this modern approach to service provider management, the maintenance requirements are made digitally available by the external TBM facility managers. They receive the respective orders at an early stage and with a clear overview via the portal. This means they are able to carry out the scheduling and assignment of orders and optimal planning. For DFS, the advantages lie in ensuring data sovereignty, maximum transparency of maintenance services carried out and realistic mapping of technical systems in their own SAP system.
M&P BEGIS and DFS plan the future
With this solution, DFS digitally processes more than 400,000 orders for services in the field of building and supply technology every year. The commissioning, verification and billing of orders are largely automated. The objectives for this module listed above have been fully achieved. In further steps, the non-cyclical additional orders and the commissioning of expert inspections will now be integrated into the system.
DFS is making great strides on the challenging path towards digital transformation of maintenance. ‘Industrial Internet of Things’ and ‘Predictive Maintenance’ are two further pilot projects that DFS is implementing to develop innovative digital concepts. M&P BEGIS looks forward to continuing to support DFS in line with the motto of DFS Technik – ‘WE ENABLE FUTURE’.
Simon Krienke, Head of Maintenance Solutions at DFS Deutsche Flugsicherung GmbH, says: ‘M&P BEGIS GmbH fulfilled the contractually agreed services in every phase of the Paperless Maintenance projects in their entirety. Not only were they carried out within the given time and budget framework, but the implementation team also listened carefully to the departments and took their technical requirements, which had arisen in the context of iterative development processes, into consideration and implemented them in short sprints. This was decisive for user acceptance and shows that digitisation can only succeed in the context of cooperation between implementation partners, departments and transformation teams.’
M&P BEGIS supported DFS as a reliable partner during the relevant implementation and during the hypercare phases. The high level of technical knowledge, coupled with the determination of the M&P BEGIS team to achieve the best result for the customer at all times, was decisive in the successful nationwide roll-out of the respective business process.
Back to the future: the launch of paperless maintenance
M&P BEGIS and DFS have proven to be ready for take-off from the SAP standard with their paperless maintenance projects, the digitisation of central service and maintenance processes. Which targets will be achieved next? You’ll have to wait and see. In the meantime, find out about the beginning of our journey together.